第2回 FPM-Trinity向け設計環境への取り組みと新しいモノづくり環境への挑戦
2020年07月09日
株式会社図研 技術本部の長谷川です。第1回「電子デバイス3Dプリンター FPM-Trinity試作サービスのご紹介」の後半でも少し紹介しましたが、引き続き株式会社FUJI様が独自開発された電子モジュール製造装置「FPM-Trinity」に向けた設計環境への取り組みと新しいモノづくり環境への挑戦についてお伝えしたいと思います。まず初めにCR-8000は、「電子機器のシステムレベル設計・検証、製造支援」を開発コンセプトとして掲げており、小さな電子部品から大きなシステムまでの設計と検証、そしてモノづくりのための製造用データ作成を支援する3D電気系設計プラットフォームです。従って、理想を言えば「どんな電子機器の設計もできるようにしたい」、というのが開発者の思いです。
これまでに、プリント基板というカテゴリーを離れ、平らではない電子機器の代表格であるMID(Molded Interconnect Device)の設計にもチャレンジしてきました。残念ながらまだ自由曲面をもった筐体の設計はできませんが、平面の集まりである部分のMIDに関しては図2のような設計データ作成ができるレベルになっており、MID設計の可能性を秘めています。なお、FPM-Trinityは3Dプリンターの技術を使うため、絶縁樹脂、電気回路導体、電子部品をすべてシーケンシャルに積み上げていくプロセスとなり、基板系CADとの親和性がよいといえます。メカCADは3D形状を自由にデータ化できるという意味で汎用性は高いものの、電気回路を認識することができないため、基板系CADに一日の長があります。
3Dプリンターによる基板製造の課題
プリント基板は、銅張積層板にマスクレジストを貼り、銅箔をエッチングして製造するプロセスが一般的です。このため設計工程では、銅箔をエッチングするためのマスク設計を行い、ガーバーフォーマットなどでCADから出力されたマスクデータを製造現場に送り、マスクツールとして使います。これに対して3Dプリンターで電子デバイスを作るためには、FR-4などに代表されるガラスエポキシ材料に相当する絶縁樹脂の3Dプリント、エッチングで形成する銅箔パターンに相当する電気回路導体のプリント、さらに電気回路導体を多層にするための層間接続ビア形成のためのデータが必要となります。しかし、一般的な基板CADからは導体パターンやビアのデータ出力はできますが、絶縁層のデータは出力できません。そもそも基板CADでは、絶縁層の形状を設計するという概念がないのです。
なお、FPM-Trinityでは電子部品を基板内の任意の層に配置することが可能です。このため、いわゆる部品内蔵基板と同じ構造に対応できるのですが、部品実装データ、特にZ軸方向の座標情報をどのように出力してFPM-Trinityの自動実装機を制御させるかなど、大きな課題も残されています。
一般的な基板CADによる設計フロー検討
当初、FPM-Trinity向け設計はメカ系CADで行われていました。簡単な回路や、評価用のTEGパターン(Test Element Group:設計・製造上の問題を見つけ出すための評価用基板)であれば十分設計が可能でした。しかし、図4のように回路が複雑な場合、電気的な接続検証ができないと配線パターンが正しいことを担保することが難しいのです。特に設計完了後に一部変更を加えたような場合、回路が本当に間違っていないか目視ですべて検証するのは現実的ではありません。
そこで、初期検討として一般的な基板CADを使ったFPM-Trinity向け設計のフローを考えてみました。基本的な構造設計はメカCADで行い、電気的なパターン設計部分のみを2Dの基板CADで分担するという考え方で進め、最終的な製造用データはメカCADから出力するという流れです。しかし、この設計フローでは、メカCADとのデータ受け渡しに時間がかかります。さらにメカCADにて製造性チェックを実施して不具合がみつかった際、基板CADに戻って不具合修正、再度データの取り込み、再チェックの繰り返しになるなど手戻りが多く発生して効率が悪いという結果が分かりました。
Design Forceによる設計環境とトライアル設計
現在FPM-Trinity向け設計に一番適していると思われる「CR-8000 Design Force」を使って、設計環境の構築を進めています。Design Forceの特徴である3D表示、マルチボード設計・検証、エレメカ連携設計、豊富なデータ出力機能、カスタマイズ機能などを余すところなく駆使しています。Design Force開発者が当初想定していないようなところまで機能を使いこなすという、運用技術も大きなポイントとなっています。
図5は、Club-Z:「指先にのる小さなデバイスでIoTを始めよう!」で連載している「Leafony」というIoT向けオープンイノベーション・プラットフォームの設計をFPM-Trinityの製造プロセスルールを使って実現したものです。前回では、センサリーフ(Leaf)のみをFPM-Trinityの製造で置き換えた事例を紹介しましたが、今回はマイコンリーフ、USB電源リーフ、BLE通信リーフを追加で設計しました。4つのリーフがLeafonyバスと呼ばれるコネクタで上下接続されている状況ですが、Design Forceのマルチボード設計環境でシステム全体のネットを検証でき、エレメカ連携設計の詳細形状部品の表示を使って、上下リーフ間のクリアランスチェックを行ったり、3D筐体形状を持たせたまま面付け配置設計を行ったり、3Dエクスポート機能を使って、FPM-Trinity向けに最適化されたデータ出力したり、といったことが可能となっています。
プリント基板の置き換えではない分野への挑戦
3Dプリンターでつくる電子デバイスは、技術紹介をすると非常に興味を持たれるのですが、いざ何かを試作しようと考えてみると適当なモチーフがなく、過去にプリント基板で実現されていたものの焼き直しになることが多いのが現実です。正直、プリント基板の製造プロセスはモノづくりにおいては理想的で、長い間時間をかけて進化してきたこともあり、それを置き換えることができるものはすぐには出てこないでしょう。FPM-Trinityもプリント基板を置き換えるものではなく、どちらかといえばプリント基板の弱点を補うもの、新しい価値を創造するものであるべきと考えています。例えば、高価な治工具代をかけて数個の初期サンプルを試作したくないとか、非常に守秘性が高く社外に情報を出したくないとか、プリント基板では構造上実現しにくい構造とか、このような時にこそFPM-Trinityの価値が活きてくると考えています。図6は「立体的な指輪型センサ」で、プリント基板を入れ込むスペースがないような構造に適用した例です。
また、新しい展開として非電気分野とのコラボレーションによる新しいモノ・価値の創出ができることに期待を寄せています。今はスピーカーが知能を持っている時代ですから、白物家電がインターネットに接続されても誰も驚きません。今後は洗面台やお風呂などが知能を持ったり、筆記具、化粧品、バッグ、靴、傘などがインターネットに接続されたりする時代になるかもしれません。その時に、思いついたアイディアを気軽に試作して使ってみる、第三者にみてもらい感想を聞くという行為は重要になると考えています。こんな時にこそ、数日で設計でき、ひとつから試作ができるFPM-Trinityは強みを発揮するでしょう。また、新しい業界同士、複数のモノづくりプロセスの融合という考えも貴重だと考えています。お互いに得意な分野でコラボレーションして、新しい価値を創造していくことは今後さらに重要性を増すと思っています。図7、図8は、一般的な樹脂造形用の3DプリンターとFPM-Trinity(樹脂3Dプリンター+電気回路のプリント+部品の自動実装)とのコラボレーションで実現した「光るマニュキュアスタンド」です。透明な筐体で作ったボディに、FPM-Trinityで製造したLED回路基板を埋め込むことに成功しています。このように、”こんなものがあったらいいな!!”というアイディアをすぐに実現することができるのが、3Dプリンターで電子デバイスを作る一番のメリットではないでしょうか?
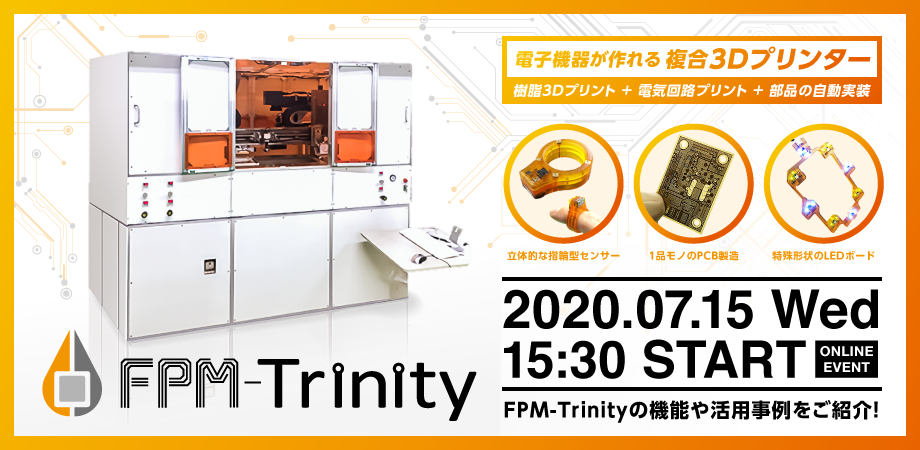
【7/15(水) 15:30~17:00、FPM-Trinityのすべてをご紹介するWebinarを開催!】
本連載でご紹介している株式会社FUJI製のファンクショナル3Dプリンター「FPM-Trinity」。今回ご紹介したDesign Forceでの本機向け設計環境の詳細、本機と樹脂3Dプリンターの2台でつくるハイブリッドアディティブ製作事例、試作サービスの受付けなど、その魅力を余すところなくご紹介するWebinarを、DMM.make AKIBAより生配信します! ぜひご聴講ください。
お申込みはこちらから:
https://fpm-trinityonline.peatix.com/
(イベント・コミュニティ管理サービス “Peatix”サイトです)