同時並行設計の活用で“求められる特性をどこよりも早く”
2016年05月25日製品の多機能小型化、高性能、省電力化など、消費者のニーズが高まる中、求められる基板も高密度化、高周波化、低電圧化が進み、作るのが難しくなっています。各基板設計ビューローはそのような時代をどのように乗り切ろうとしているのか。図研製品を使った各社の取り組みをご紹介します。1回目は、株式会社アレイ様によるDesign Forceの同時並行設計の活用事例です。
社員を犠牲にしない超短納期を実現したい!
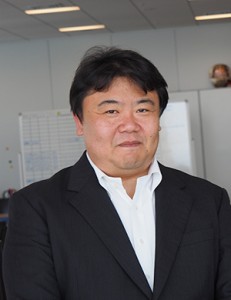
株式会社アレイ
代表取締役 堀部 基至 氏
プリント基板の製造メーカで働いていた際、納期に一日遅れたことがあり、その一回でその後仕事をいただけなくなったことがありました。この経験から超短納期のニーズを強く感じ、プリント基板を世界一早く作りたいという思いで株式会社アレイをつくりました。高周波回路や電源回路は品質だけでなく、特性も求められます。そのため「求められる特性をどこよりも早く」をコーポレートメッセージとして掲げています。
しかし超短納期を実現するにあたり、設計者の深夜残業や休日出勤、熟練した設計者への作業の偏りなど様々な問題があり、このまま超短納期を推し進めていくと2交代の24時間体制を取らざるを得ない、という経営課題を抱えていました。
社員の生活を犠牲にしない超短納期はどうしたら実現できるか。時間だけでなく設計者の健康、厳しくなっている労働法も考慮しつつ利益をあげるには、ビジネスモデルを考え直す必要があると考えました。そこで同時並行設計に目をつけ、6社ほど検討した中から、純国産で、大手を顧客に抱えている安心感から、図研の Design Forceを1年前に導入しました。社内展開はまだ進行中ですが、この同時並行設計を使いこなせば、超短納期や作業の平均化を進められるだけでなく、設計者の教育にも使えるため、悩んでいた経営課題を解決するきっかけとなるツールと考えています。
納期短縮の実現には複数人数での設計を考えますが、Design Forceの同時並行設計を選択する利点を、従来型の分割設計と比較してご説明いたします。
同時並行設計なら、分割設計より格段に工数削減できる
従来型の分割設計では、1案件の設計データを分割して各担当者が別々に設計します。例えば下図の左側のように基板や回路を分割し、一人が上部の設計を行い、もう一人が下部の設計を行うことになります。一方Design Forceの同時並行設計(下図右側)では、データを分割しないで設計することができます。
従来型の分割設計における部品配置では、各担当者のおおよその配置領域を決めて作業するため、高密度実装が予想される基板での対応が難しくなります。限られた空間に回路を詰めながら納める必要があり、分割設計ではさらに領域が制限されるからです。そのため従来型の分割設計を採用する場合でも、部品配置は一人で行う、または一人である程度レイアウトを決めた上で詳細は複数人数で分割して進めることが多いと聞きます。
従来型の分割設計における配線では、分割領域に跨る配線を基板全体のイメージをもちながら設計する必要があります。さらに各担当者の配線が終わった後は、分割したデータを1つに合成しなければなりません。データの合成やGNDの強化_(ベタ・ビアなど)、シルク編集からDRC(デザインルールチェック)などの残り作業は1人で行うことになります。
右図は弊社実績を元に算出した設計時間(2人の場合は期間)の比較です。
単独設計で250h程度かかる案件を従来型の分割設計(2人分担)を行うと約180~200h程度で終えることができました。分担することで配置配線作業の大半を2人で作業できますが、合成による手直し工数がかかるため、単独設計からは経験的に20%程度の期間短縮という印象です。一方でDesign Forceの同時並行設計(2人同時)で行った場合、約50%の期間短縮で終える事ができました。
Design Forceの同時並行設計では、配置・配線、シルク編集といったすべての作業を1データで設計しますので、合成作業の工数がかかりません。さらに、担当領域に制約を感じず単独設計の感覚で作業できる事が効率アップにつながっていると感じています。
設計者の得意分野が活きる同時並行設計
Design Forceの同時並行設計の部品配置や配線時におけるメリットを、具体的な事例をもとにご紹介します。
① 部品配置
設計者AはBGAの引き出し、設計者BはDDR周りの配置を行っています。
この回路では等長配線を考慮する必要がありますが、他者が既に配置した部品の移動が可能ですので、基板全体を見渡して配線長合わせのスペース確保を検討できます。基板全体を見渡しながら、回路の流れを考慮した部品レイアウトができること。電源回路の経験に長けているなど各担当者の得意分野が活かせる利点もあります。
② 配線
設計者Bは右下のコネクタからの引き出しを行っています。設計者AはDDRからの引き出しをしているところです。
同時設計の特徴として、担当者が位置的に離れたところを設計している場合でも、相手の配線めがけて配線接続をすることができます。また設計者によってパターンの引き方が違う箇所がある場合(例えば、類似回路で電源の引き出しビア径が異なるなど)、このままですと基板全体を見渡した時にちぐはぐな設計になります。
Design Forceの同時並行設計では他者の設計を随時確認しながら作業ができるので、複数人数で設計をしていても基板全体のレイアウトをある程度統一できます。配線要求がある箇所を専任で行い、先行して検図出しができれば、修正の戻り作業も削減できます。
操作感覚については下記のムービーをご覧いただけば分かる通り、特に動作が遅いと感じることは有りません。
技術伝承にも役立つ
パターン設計者は、単にCAD操作ができるオペレーターでは通じない世界だと思います。もちろん、CADを正確に操作して間違いのない設計をする前提です。加えて、高速信号の場合はこのように配線した方が良いなど、仕様を考慮した設計が必要でので、回路についての基礎知識が必要です。
しかしここからが難しいところであり、実際どうレイアウトするかは設計者のスキルやセンスに委ねられています。時間をかけてでもきれいに回路をまとめる人もいれば、スピード重視で雑に思える設計をする人もいます。ショートや製造不具合につながるようなエラーは、CADのDRC機能で検出できますが、それ以外は配慮できているでしょうか。例えば信号配線が終わり電源・GND層のレイアウトをした結果、プレーンスリット上を高速信号配線が跨いでいると気づく事があります。信号配線ばかりに気を取られて、回路全体のレイアウトを考慮していないと起こりうる事ですが、CADのDRC機能では検出できません。リターン電流考慮といった事は回路によっては特性に大きな影響を与えますので、設計品質という目線では重要なところです。
設計会社にとりましては設計ノウハウ=設計品質とも言えますが、こうしたノウハウは主に個人に蓄積してしまうので、他の人に伝えてゆくという事は難しいと感じておりました。
右図の左下の写真は弊社の社内レビューの様子ですが、設計途中や設計後に「この回路はこういう風に引いた方がいいのではないか」「この電源回路はこう設計しなさい」など意見交換や教育の場を設けております。また設計ガイドラインを作成して、過去の不具合や改善点について周知しております。しかし書面や口頭では伝えきれないのも現状です。それがセンスと言えばそれまでですが、Design Forceの同時並行設計で共同体験をする事で、こうしたノウハウを修得しやすくなるのではと考えました。
Design Forceの同時並行設計では、他の設計者が作業をしている様子をみながら、それに倣うことができます。設計途中に問題となるレイアウトを見つけたなら、それを指摘することも容易です。こういう風に引いた方がいいよと実際にやって見せることができるのです。
例えば先輩と後輩が組んで部品配置をしているとします。先輩は電源周りを担当している後輩がどのような設計をしているか気になり作業箇所をみたところ、基板全体のレイアウトを意識していない様子です。このままでは配線経路が複雑になり、電圧降下やノイズ源となる危険が予想されました。そこで後輩にどうしてこの配置なのか聞くと、目先の配置だけに集中していて後工程の配慮ができなかったという事です。
新人時代を思い出してほしいのですが、先を考えずに作業することが多かったと思います。ある程度経験を積むと先が想像しやすくなりますが、経験年数が全て解決するわけでもないようです。教える側としては習熟度の把握のほか、作業の丁寧さや注意深さなど個人の性格にもよる部分も理解し、適切なアドバイスをしてあげる必要が有ります。
Design Forceの同時並行設計では、実案件を担当しながら、見て覚える事ができます。熟練した設計者の場合でも、同僚や後輩の設計から学べる部分も有るかと思います。ノウハウ伝達を効率よく行う事で、設計者全体のスキル平均化が望まれますので、設計者の負担の偏りも解決されるのではと期待しています。
簡単ではありますが、納期短縮と特性確保という目線で同時並行設計が有効であるということをご紹介しました。
「求められる特性をどこよりも早く」
現在は消費者のニーズがとても厳しくなってきています。携帯電話の進化を考えた時、25年くらい前にはポケベルが流行っており「4649(よろしく)」など数字で意思伝達をしていた時代を懐かしく思います。それが数年経つとPHSや携帯電話が普及しはじめ、さらに現在はスマートフォンやウェアラブル端末へと進化しました。単なる通話機能を超え、カメラ・ゲーム機・健康器具などを1つにした小型複合機となっています。こうした消費者のニーズ実現の為に、プリント基板はより高密度化し、扱う回路が高周波化したうえに、低電圧化の要求を満たす必要が有ります。
基板が高度化にともない、求める特性や各種製品規格達成の阻害要因が増している一方、試作の繰り返しや対策工数を価格に反映する事は難しい現状です。
前述で設計スキルの平均化について触れましたが、「こういったパターンだったら大丈夫だろう」といった経験則だけでは求める特性が確保できない時代になっているのではないでしょうか。
弊社の今後の展望として、納期短縮という目的で現状2台の同時並行設計を3台体制にすることを検討しています。さらに特性確保という目的で既に運用しているシミュレーションをより強化してゆきます。設計中に解析できるDesign Force SIなどのツールを取り入れる事も検討してゆければと思います。弊社では「求められる特性をどこよりも早く」というコーポレートメッセージを掲げ、設計を行っています。当然設計を早くやって、価格が安ければよいのですが、何よりも大事なのはお客様が望むものを提供するということです。
また、今年度の社内スローガンを「繋げる仕事をする」としました。次に繋げる仕事をするためには、単にやって終わったという満足感だけではダメです。品質、そして特性を優先した上で短納期の対応をする。そうしたことを目標として設計をしています。
株式会社アレイをどうぞよろしくお願いします。




■ 株式会社アレイ
設立:2001年3月1日
資本金:3,250万円
所在地:横浜市西区高島1-1-2 横浜三井ビルディング15F
従業員数:15名
使用CAD:図研 CR-8000 Design Force Ver.2015、CR-5000 PWS Ver.24、Mentor Graphics PADS Layout V9.5
ご紹介ページ ⇒ https://www.mmjp.or.jp/ssl.array-net.com/lp/