Club-Z読者の皆さま、こんにちは。
こちらの連載では、「製造部門の業務をデータ活用によるスマート連携・効率化していく取り組み」へのヒントとなるような情報をご紹介していきます。
製造部門の業務効率化には、開発部門からのデータ受け渡し方法も変革していくことが重要になりますので、システム管理部門、開発部門の方々にもぜひともお読みいただきたいと思います。
それではどうぞよろしくお願いします。
ここ数年で、モノづくり全体にわたって従来は想定していなかった大きな変革に取り組む必要がある状況になってきたと思います。例えば、カーボンニュートラル/脱炭素に伴う流れ、自動車のEVシフトやコロナ禍以降の働き方の変化のほか、米中間での政治的対立、ウクライナ紛争など外的要因に伴う部品や設備の調達調整など、Club-Z読者の中にも、何らかの対応を迫られた方がいらっしゃるのではないでしょうか。
このような状況下、図研では工場での生産品目の再編や、開発部門から製造部門までを横断する形でデータを活用した業務効率化に取り組みたいと、ご相談いただく事例が増えています。

図.工場での生産品目再編への取り組み例:生産バランスの最適化や工場稼働停止、
部材供給停止リスクなども加味し、複数工場で製造できる体制
特に、開発部門から製造部門へのデータ引き渡し方法については「かなり以前に取り決めたルール」から変更/更新されずに現在まで引き継がれていることも多く、そこが全体を俯瞰した際のボトルネックになり、DX推進 を難しくする要因になっています。
*開発部門視点:アートワーク設計委託先が複数&基板製造委託先が複数ある
→すべての製造先に対応したデータにするためには新たなフォーマットへの切り替えが難しい
*製造部門視点:今までとは異なる製品、場合によっては他社製品の製造受託なども行っていくため、
さまざまなケース/データに対応できるようにしていく必要がある
→すべての受領データが均一化されることが望ましいが、依頼元の環境が影響するため、難しい
表.主な製造先(3拠点)と対応フォーマット例(〇:可、△:要確認、×:不可)
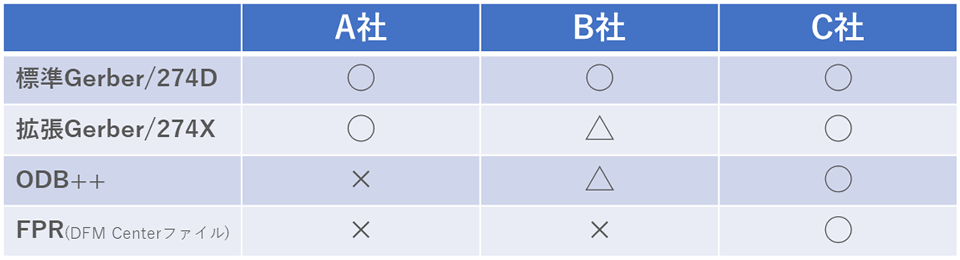
基板仕上がり品質やコスト、納期の面よりA社、B社、C社それぞれとは今後も取引を継続
→ どこでも対応可能な 標準Gerber/274D形式での運用で落ち着いている
業務改革にあたっては、会社として組織変更を行い、専門の組織を中心に横断的に取り組みを進めていることも多いですが、この連載においてはその前段階として製造部門だけで取り組める内容なども織り交ぜて紹介していきます。
具体的には、プリント基板製造およびプリント基板への部品実装における製造部門エンジニアの業務視点でのよくある課題 、そして図研製品(DFM Center)を活用した場合の解決策について、ご紹介します。
また、製造段階での課題の中には設計段階で対策し未然防止できるものもあります。
電気設計者の皆さんは、基板設計において、EMCノイズ、熱、高速信号配線などのさまざまな要件を短期間で満たすため、CAEツールも含めてCAD機能を徹底活用することに取り組まれていると思いますが、製造性検証システムの活用についてもとことんご活用いただけるよう、本連載が少しでもお役に立てるように頑張ります。
本連載では、主に以下のような課題、ニーズをご紹介していきます。
<基板設計段階での基板製造性、部品実装性検証に関連する課題>
✔ チェックシートで目視チェックしている項目があり、ヌケモレが起きている。 自動化して作業効率やチェック品質を改善していきたいと考えている
✔ 前任者から引き継いだチェックツールがあるが、どのようなルールが設定されているのかブラックボックス化されていて分からない
✔ 製造委託先の工場が複数あるが、製造ルールは各々少しずつ違っている。そのためすべての委託先を満たすルール値でチェックしているが、管理が大変
✔ 転注先選定は、仕様的に問題なく生産できることを確認した上で、コストを考慮して行いたい
✔ 製造や実装拠点との設計データ修正箇所のやり取りで、ドキュメントとCADデータとを見比べるのが煩わしい
<FPC製造準備、製造設計業務に関連する課題>
✔ 製造準備段階のパネリング作業、製造工程検討、治工具検討を行うシステムがなく、すべて手作業で行っている。また、各作業に時間がかかり、セットメーカーへの見積もり提出に時間がかかる
✔ 製造準備段階の作業には経験や高いスキルが必要で、海外の設計部門が立ち上がらない
✔ 見積もりに必要な支給データの情報収集をCAM編集者へ依頼しているため、見積もり作業をすぐ始めることができない
✔ セットメーカーから支給されるデータはGerberやDXFが多く、データの確認、工程検討などの作業、またセットメーカーへの修正依頼などのやり取りにも手間がかかる
✔ 見積もり検討を行った材料情報や工程情報などを製造設計(治工具設計)で活用したい
✔ コストダウンのため、パネリングの品質を向上させたい
<部品実装準備に関連する課題>
✔ 実装データを作成する際、受領データの形式が一定ではないため、多くの手作業を入れて実装部品の工程別仕分けを行っている
✔ 各実装機、検査機用に部品登録しており、無駄を感じている
✔ 受領データがGerberとなるため、メタルマスク開口の変更指示や編集内容の確認が充分には行えず、トレーサビリティも不安
✔ それぞれの作業が属人化されており、コロナによる長期休養時など、生産効率が各段に下がってしまうトラブルが発生した
✔ もしかしたら流用できる治具があるかも知れないが、それを調べる手段がないため、都度新たに作成している
✔ 自社開発ソフトを含めてカスタム対応しているが、今では仕様が不明瞭で機能拡張、変更の妨げになっている
それでは次回以降、
・設計段階での製造性、実装性検証による歩留まり向上や手戻り発生改善
・FPC製造準備、製造設計業務における課題と解決策
・部品実装準備業務における課題と解決策
について順次ご紹介していきますので、どうぞご期待ください!